Flux Cored Wires - Introduction and Advantages
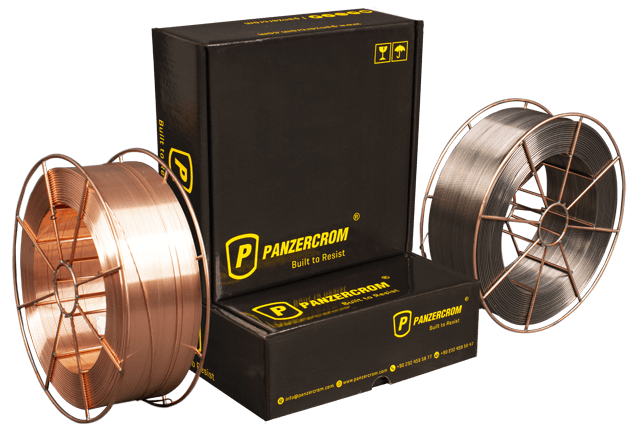
What Is Flux Cored Wire? What are the Advantages?
Flux cored wires are welding wires manufactured by filling a steel strip in pipe form with various chemical compounds (core). Flux cored wires can be used with any type of GMAW machine with or without gas shield depending on the product type. Name of the process is “Flux Cored Arc Welding (FCAW)”Cored wires can be manufactured in two types as folded and seamless types. Folded flux cored wires are manufactured by bending strips in a u-shape like a seamed pipe manufacturing process and filling a powder core (a formulation with alloy) in it and then rolling it as a thin pipe. Seamless flux cored wires is manufactured by filling the core in a seamless pipe steel band. Flux cored wires were developed at the beginning of the 1960s in the U.S.A with the expectation of welding capabilities in all positions and to use single product in all manufacturing and alloy types.
However, material science kept rising and high tech materials started to take stage on welding scene. Variety of base materials made it impossible for this product to be “one product for all alloy types” idea which was one of the main purposes of this products development.In the following 20-years after cored wires first development, it was discovered that cored wires had other advantages over conventional GMAW and SMAW. Usage area and consumption of cored wires are still increasing today. Regardless of hardfacing & maintenance-repair welding or joint welding, various companies are no longer using GMAW or SMAW.
Advantages of Cored Wire Welding Method:
- It will provide 10-40% manufacturing speed increase with high deposition speed (weld metal/min).
- It provides welding position capability in every position.
- With low heat input, it ensures high mechanical properties and hardness with perfect microstructure compared to conventional methods.
- Open-arc (without shielding gas) welding is possible.
- Cost per kg is more economical compared to solid wire in medium and high alloy product groups.
- Manufacturers can control product formulation (core content). Thus, cored wires weldability is better than some GMAW wires
- This method is faster than the electrode method. Metal-cored formulation is slag-free and suitable for multi-pass robotic applications.
- Stub loss creates significant extra costs while using stick electrode method. Flux cored wires are manufactured as 15/25kgs spools or 250/500kgs drums like solid wires and there is no stub loss.
Discover Panzercrom® welding consumables; https://www.panzercrom.com/en/flux-cored-wires-for-hardfacing/
Discover our focus industries; https://www.panzercrom.com/en/cement-and-concrete-industry/
You can contact us from https://www.panzercrom.com/en/contact/ for more information about our wear solutions, wear plates and welding consumables.
Follow us on social media;
Linkedin: https://www.linkedin.com/company/panzercrom
Instagram: https://www.instagram.com/panzercrom/
Facebook: https://www.facebook.com/panzercrom/